Highlighted Equipment
MAST
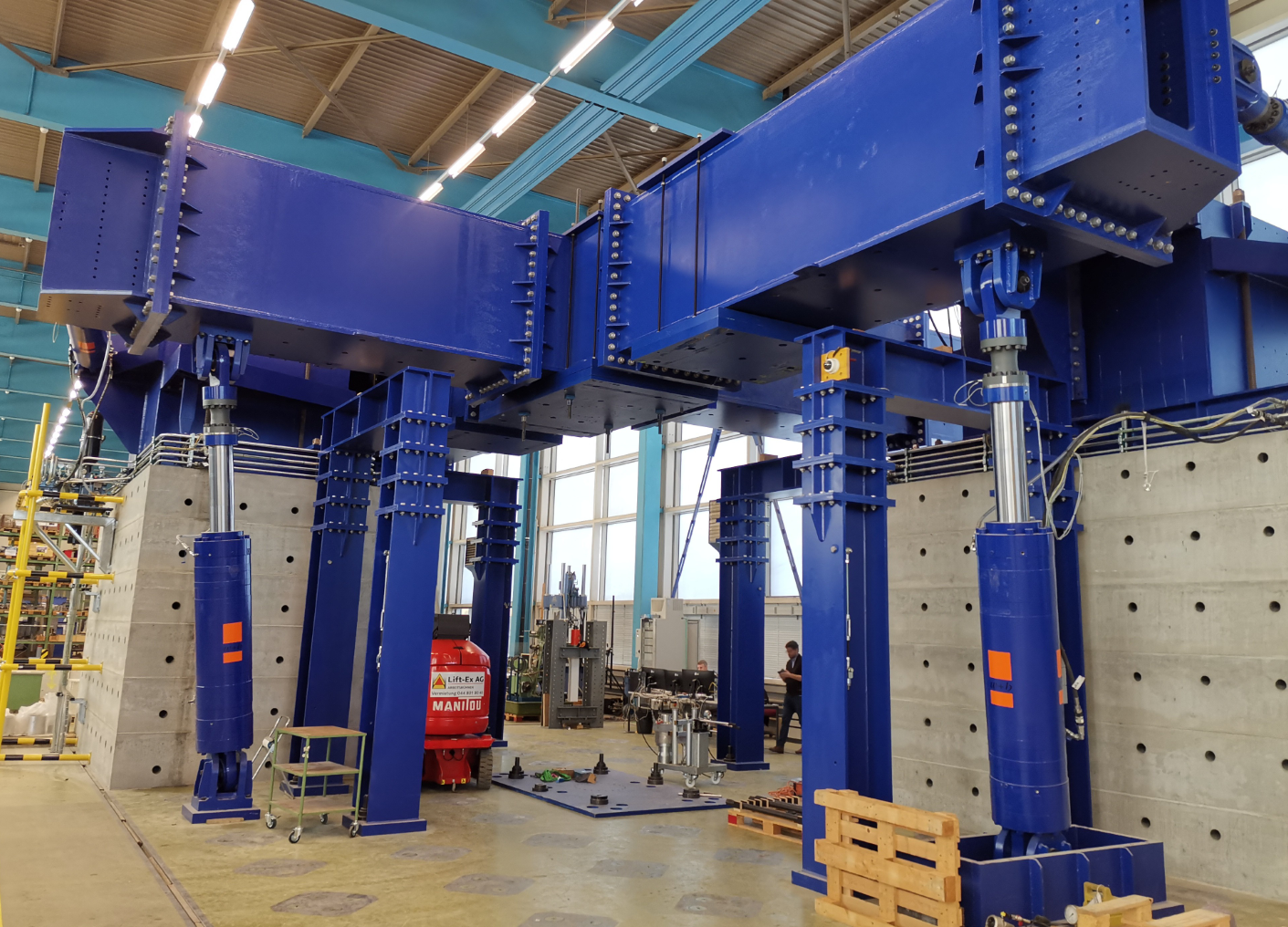
The Multi-Axial Subassembly Testing (MAST), designed by the chair of Prof. Stojadinovic, enables quasi-static cyclic tests and hybrid simulations of full-scale structural elements and sub-structures under computer-controlled 6-degree-of-freedom mechanical boundary conditions. It comprises 8 servo-hydraulic actuators reacting against the strong floor and reaction towers and one modular steel cross-head. In the long configuration, the cross-head dimensions are 15x12 m2, while its core is approximately 5x4 m2. The vertical clearance under the cross-head is approximately 4.5 m. The system is capable of applying up to 10 MN of vertical force, up to 4 MN in one and 2 MN in the other horizontal direction, and moving the specimen up to horizontal drift ratios of 7%.
LUSET
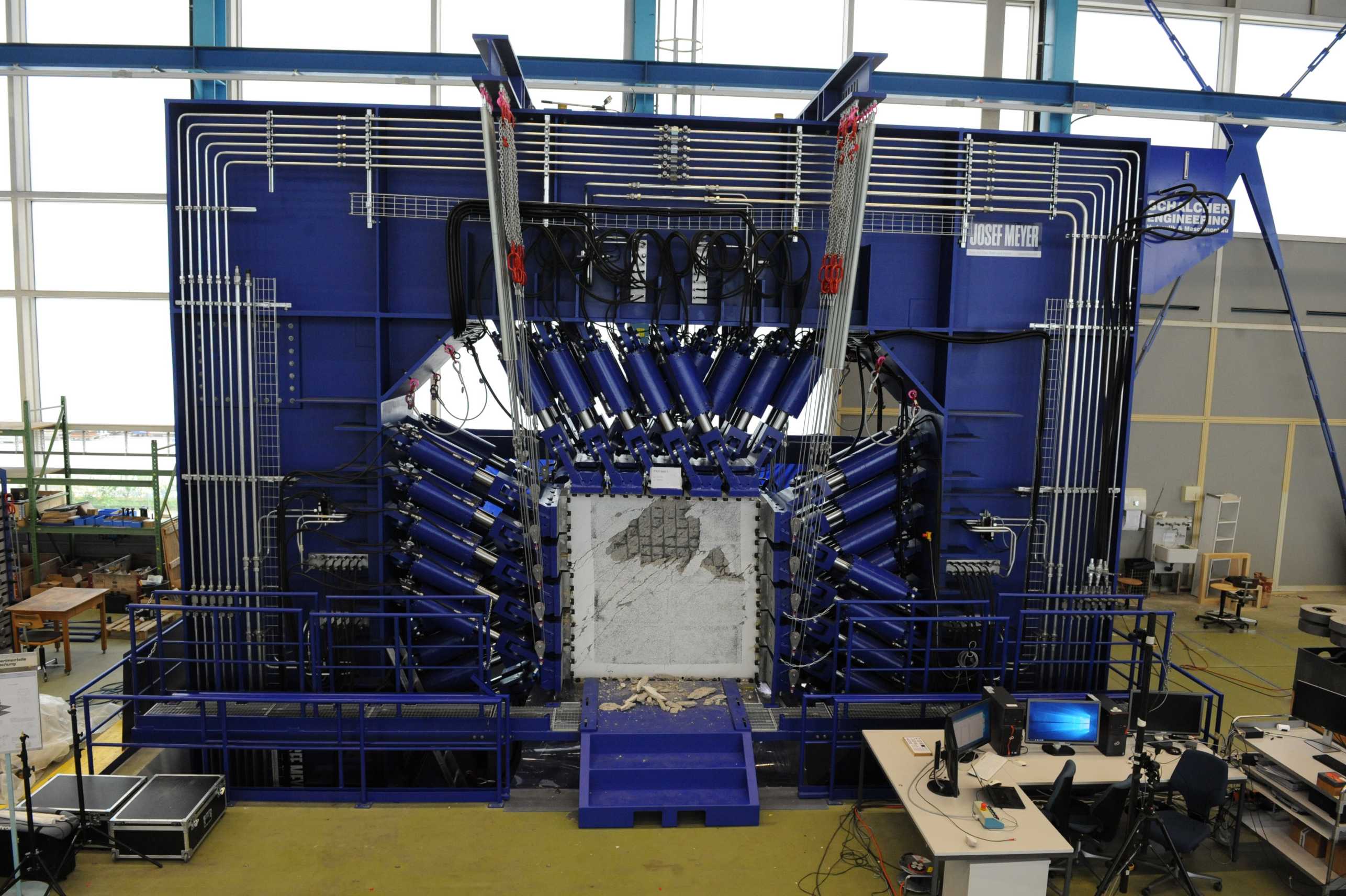
The Large Universal Shell Element Tester (LUSET), commissioned by the chair of Prof. Kaufmann in 2017, enables large-scale testing of reinforced concrete shell elements with dimensions of 2.0x2.0 m (2.20x2.20 m including connector blocks) and a variable thickness of up to 0.45 m. Well controlled, arbitrary load combinations (e.g. homogeneous or linearly variable loading by all 8 independent stress resultants of a shell element) can be introduced along the four edges of the specimen by means of 100 hydraulic actuators, equipped with spherical hinges at both ends, acting on twenty independent loading yokes. Each of the five yokes per specimen edge is loaded by one out-of-plane actuator (capacity +0.9/-1.2 MN), and four in-plane actuators (capacity +1.2/-1.4 MN per actuator), positioned at an inclination of 1:2 with respect to the outer normal of the element. More than 30 experiments were carried out in LUSET to date (12/2019).
MAD-Sim
The servo-hydraulic Multi-Axial Dynamic Simulation Table (MAD-Sim), operated by the Chair of Structural Mechanics and Monitoring (Prof. Chatzi), will be used for dynamic and hybrid testing of structural and mechanical components. The facility is intended to be placed within a climatic chamber simulating field environmental conditions.
Specifications:
- Test area 2.2 m x 2.2 m
- Specimen mass <1 t
- Dynamic range 0.8...100 Hz
- Displacement +/- (140x110x120) mm
- Velocity +/- (1000/900/1000) mm/s
- Max payload acceleration (1000 kg @ 500 mm +/- (8.5x6.5x8.0) g)
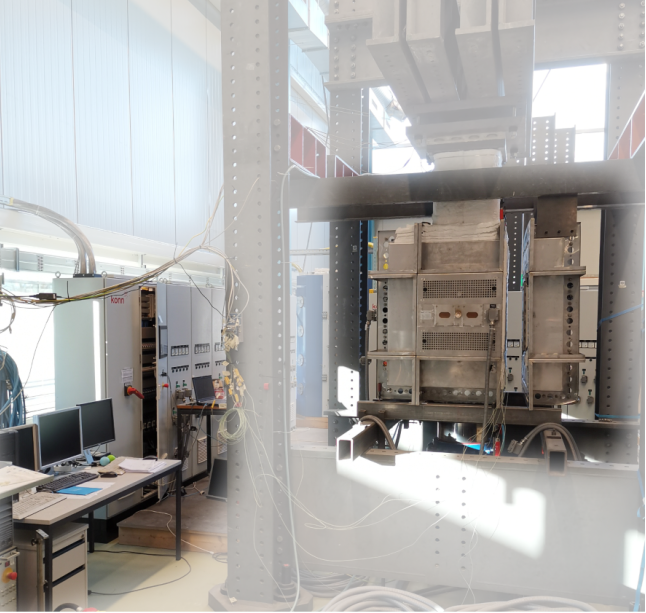
Modular-furnace tester
Furnace based on modular panels for heat tests up to 1200 °C @ 70 °C/min.
The system is used by Prof. Frangi, Prof. Taras, Prof. Stojadinovic.
- Max. 60 Panels, 40 kW/Panel, 560x560x340 mm3 in size
- Open or closed configuration
- 0.5x0.5x0.5 m=0.125 m3 minimum volume in closed configuration
- Loaded configurations possible
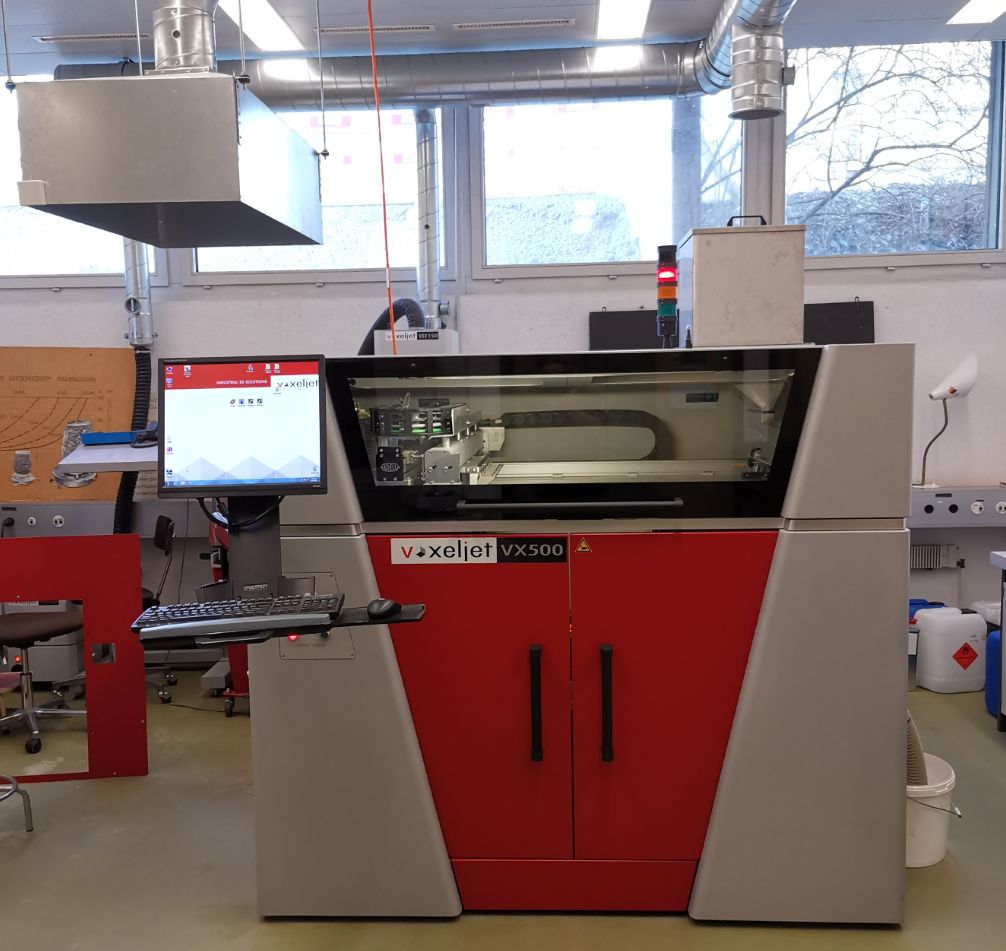
VoxelJet VX500-0025 ODB
3D printer VX500 (Voxeljet Technology GmbH, Augsburg, Germany). The job box has the dimensions (xyz) 500x400x300 mm. The job box filled with ceramic blends prints layer by layer. The STL files of the parts to be printed are imported into the machine software Rapix3D (Forwiss, Passau, Germany) and positioned in the virtual job box. After completion of the job, the parts must be cleaned with an air blower, and dried for 24 h in an oven at 40 °C.
The 3D printer is used by Prof. Vassiliou to produce reduced-scale structural components for new methods of experimental testing.